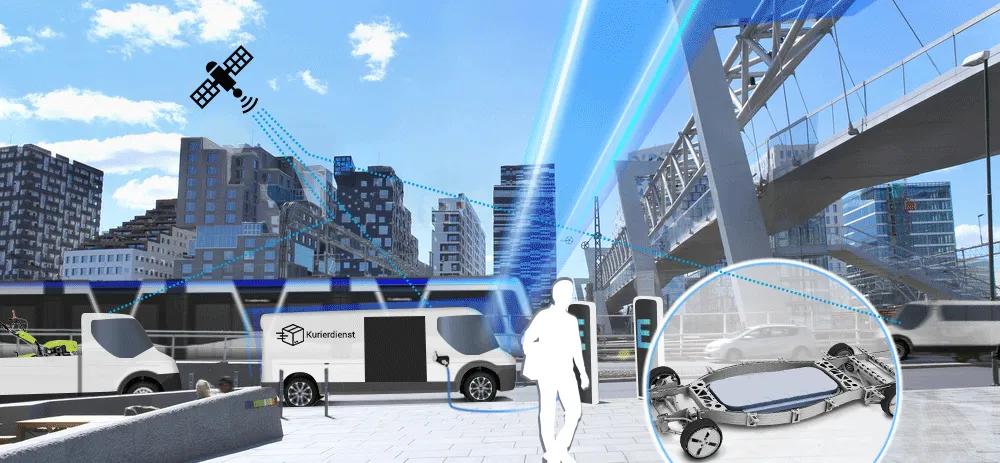
Leichtbau
3D-FiberTrain
Entwicklung eines werkzeuglosen Fertigungsverfahrens zur Herstellung großformatiger und hochbelastbarer Schienenfahrzeugkomponenten
Projektzeitraum: Sep 2023- Jun 2026 | Projektpartner: Fraunhofer IWU, Lakowa Kunststoffbe- und verarbeitungs GmbH, Siemens Mobility GmbH (assoziiert)
Das Forschungskonsortium um HÖRMANN Vehicle Engineering erforscht und entwickelt eine innovative thermoplastische Technologie, die Großformat-3D-Druck mit dem 3D-Tape-Legeprozess kombiniert. Diese Methode ermöglicht die werkzeugfreie Herstellung komplexer und belastbarer Großkomponenten für Schienenfahrzeuge, wie Frontmasken und Dachstrukturen. Besonders bei kleinen bis mittleren Seriengrößen bieten additive thermoplastische Verfahren erhebliche Optimierungspotentiale in Kosten, Zeit und Material sowie eine Reduzierung des CO2-Fußabdrucks. Der Verzicht auf Formwerkzeuge, hoher Automatisierungsgrad und der Einsatz wiederverwendbarer Materialien führen zu niedrigeren Herstellungskosten und verbesserter Ressourceneffizienz im Vergleich zu herkömmlichen duroplastischen Faserverbundverfahren.
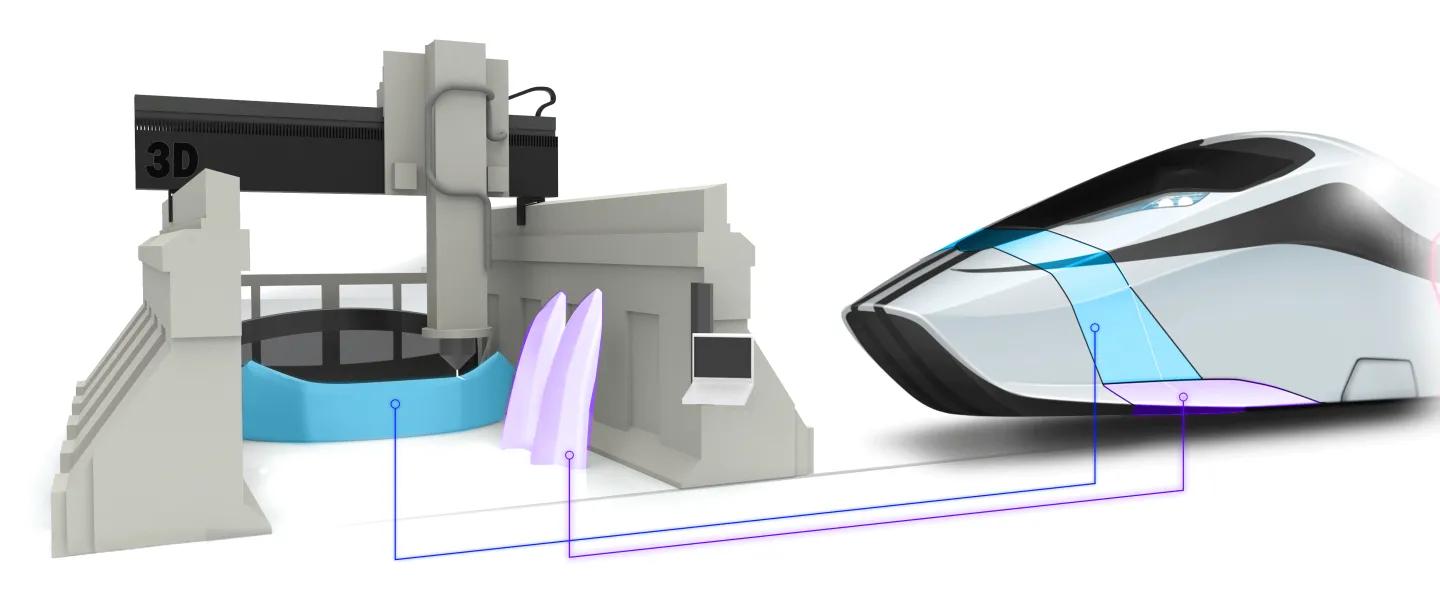
Gefördert durch:

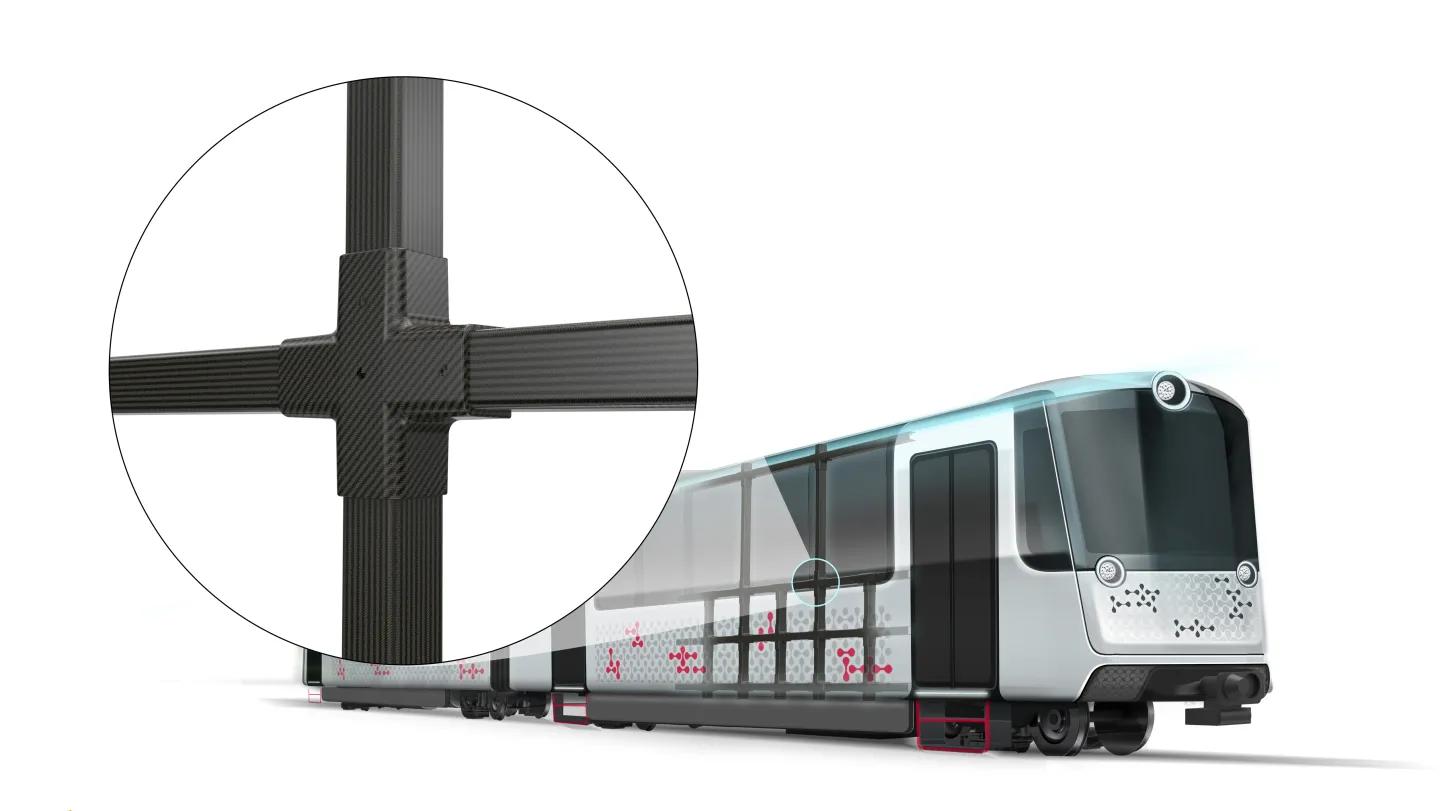
PulPro - SMC
Einsatz von Pultrusion-Profilen in Kombination mit lastpfadgerechten SMC aus recycelten Kohlenstofffasern in Rohbaustrukturen von Schienenfahrzeugen
Projektzeitraum: Okt 2023- Jun 2026 | Projektpartner: Conbility GmbH, Fraunhofer IWU, LSE-Lightweight Structures Engineering GmbH, Modellbau Roth GmbH & Co. KG, Polynt Composites Germany GmbH
Um unterschiedliche Perspektiven und Anwendungen der Querschnittstechnologie Leichtbau zusammenzubringen und weiterzuentwickeln, verbindet das F&E-Vorhaben PulPro-SMC unter Federführung der HVE GmbH gezielt Kompetenzen aus mehreren Leichtbau-Disziplinen. Mit dem Fokus serienfähigen Strukturbauteile aus faserverstärkten Kunststoffen ressourcenschonend herzustellen für die Massenmärkte auf Straße und Schiene. Ziel ist es eine Alternative zur konventionellen Methodik, die Kombination aus Schweißen und Stahlprofilen, aus pultrodierten Faserverbundprofilen eine stoffschlüssige Rahmenstruktur herzustellen. Speziell die Verknüpfung der sich nach allgemeinem Verständnis eher widersprechenden Bereiche Leichtbau, Crashsicherheit und Wirtschaftlichkeit stellt eine große Herausforderung in dem Projekt PulPro-SMC dar. Angestrebtes Gesamtziel ist die Realisierung einer effizienten und wirtschaftlichen Herstellungstechnologie für faserverstärkte Leichtbau-Fahrzeugstrukturen in einem modifizierten Pultrusionsverfahren in Kombination mit einem lastpfadgerecht verstärkten Recycling-SMC-Formgebungsprozess. Der Technologienachweis soll anhand einer realen Schienenfahrzeugkomponente geführt werden.
Gefördert durch:

LeiPo-3D-FKM
Erschließung neuer Leichtbau-Potenziale durch standardisierte Auslegung von Bauteilen des metallischen 3D-Drucks mittels FKM-Richtlinie
Projektzeitraum: Jan 2025- Dez 2027 | Projektpartner: IMK Engineering GmbH, BMF GmbH – Bernstein Mechanische Fertigung, SWM Struktur- und Werkstoffmechanikforschung gGmbH, TU Chemnitz – Professur Strukturleicht-bau und Kunststoffverarbeitung
HÖRMANN Vehicle Engineering setzt sich für die Erreichung weltweiter Klimaziele für Energieeffizienz und Ressourcenschonung ein. Im Bereich des metallischen Leichtbaus eröffnen innovative Produktionsmethoden, wie die additive Fertigung, erhebliche Potenziale zur Massereduktion. Um diese Technologie breiter zu etablieren, ist eine standardisierte Auslegung additiv gefertigter Komponenten notwendig. Die FKM-Richtlinie spielt hierbei eine zentrale Rolle, jedoch integriert sie derzeit nicht den metallischen 3D-Druck und dessen Nachbearbeitungsmethoden. Dies schränkt die Innovationskraft der Unternehmen, die nach FKM auslegen müssen, erheblich ein.
Der LeiPo-3D-FKM-Verbund zielt darauf ab, dieses Problem zu lösen und eine additiv gefertigte Stahllegierung für die FKM-Qualifizierung zu entwickeln. Dabei werden wichtige Einflussfaktoren wie Pulverzustand und AM-Anlagentechnik sowie Nachbearbeitungszustände, insbesondere Oberflächenglättung und -verdichtung, berücksichtigt. Die Anwendungspartner transferieren dieses Wissen auf repräsentative Technologieträger im Transport- und Maschinenbau und validieren es durch Prüfungen.
Gefördert durch:

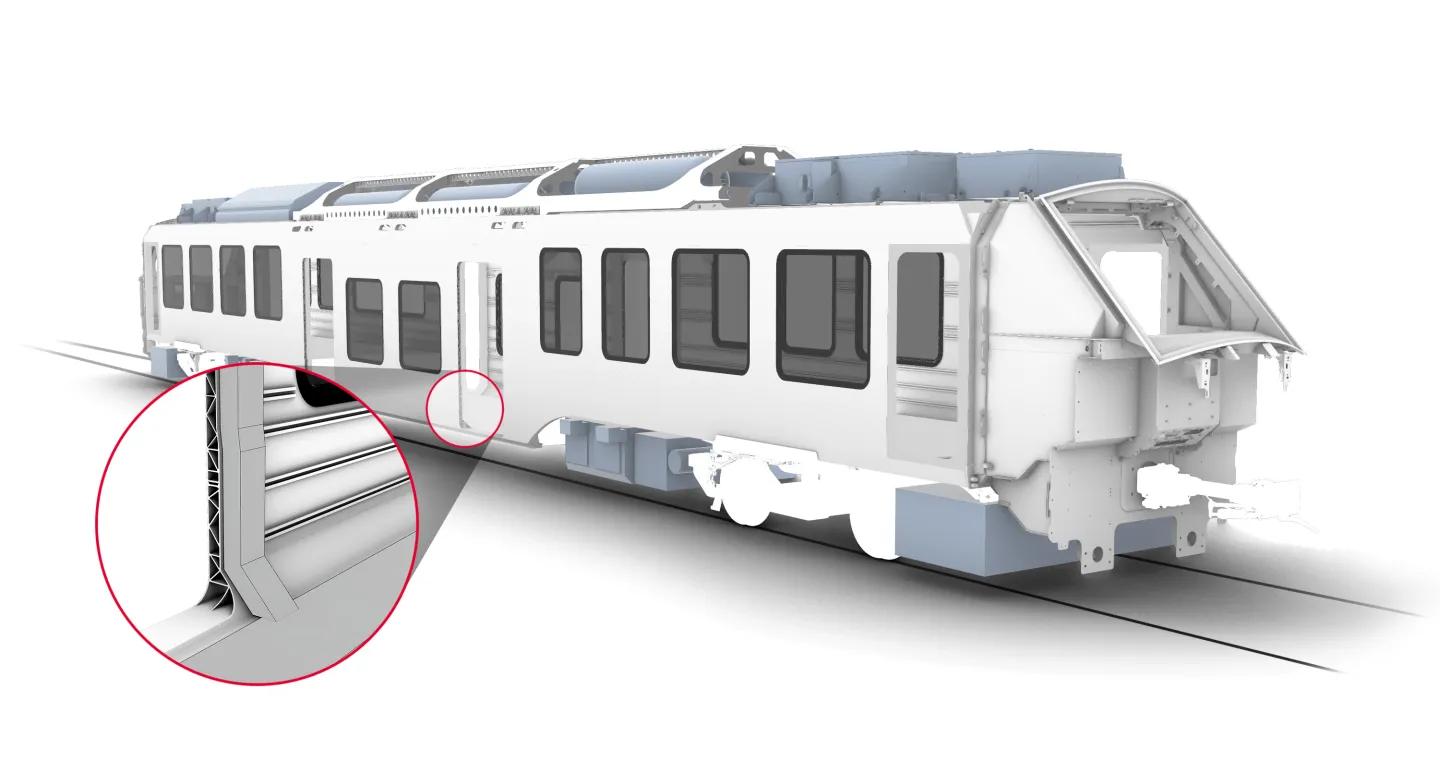
AnoWaAs - Abgeschlossenes Forschungsprojekt
Entwicklung eines neuartig und modularen Wagenkastens für Schienenfahrzeuge
Projektlaufzeit: Mai 2021 – April 2024 | Projektpartner: ALSTOM, DLR - Institut für Fahrzeugkonzepte, elemag GmbH, GSI mbH Niederlassung SLV Berlin-Brandenburg, Rausch Metalltechnik GmbH, Uni Stuttgart - Institut für Maschinenelemente, 3A Composites GmbH
Im Rahmen des Projekts wird systematisch ein neuartiger, modularer Wagenkasten für Schienenfahrzeuge entwickelt. Bezüglich Struktur und Architektur wird dieser möglichst optimal an alternative Antriebssysteme (Batterie und Brennstoffzelle) angepasst. Ziel ist es die schweren Komponenten, unter Berücksichtigung der mechanischen Wagenkastenarchitektur und dem signifikanten Leichtbau, optimal zu integrieren. Dabei erhalten Kosteneffizienz, Fertigung, Instandhaltung und Recycling einen besonders hohen Stellenwert. Anhand verschiedener Methoden wird die komplette Entwicklungskette abgebildet: von grundsätzlichen, verfahrensbasierten Packaging-Untersuchungen über Bauweisenentwicklungen, neuartige Konstruktion- und Auslegungsverfahren bis hin zu optimierten Fertigungs- und Montageverfahren und die prototypische Umsetzung beispielhafter Komponenten, wobei der Leichtbau immer im Vordergrund steht. Die Ähnlichkeiten von Nutzfahrzeugkarosserien und den Wagenkästen von Schienenfahrzeugen werden genutzt und erkannte Synergien zwischen beiden Bereichen konsequent verfolgt. Daher umfasst das Konsortium Partner, die über eine Expertise in beiden Branchen und darüber hinaus verfügen. Die Ergebnisse werden zur Stärkung der deutschen Wirtschaft im Leichtbau und zur CO2 Einsparung beitragen.
INTEGRAL (abgeschlossenes Forschungsprojekt)
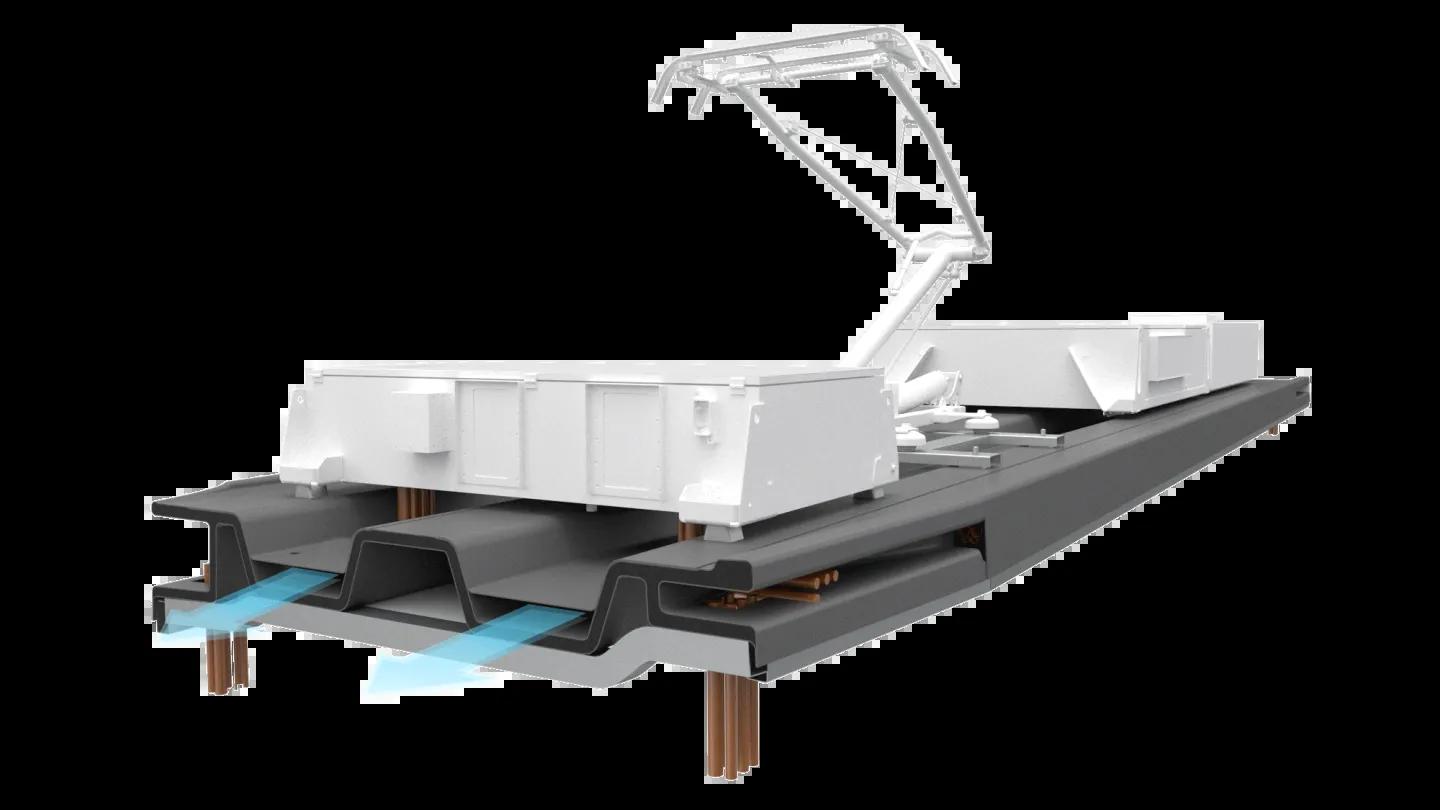
FunPul (abgeschlossenes Forschungsprojekt)
RESOLVE (abgeschlossenes Forschungsprojekt)
Im Forschungsvorhabens RESOLVE sollen nun die Qualifikation der Technologieansätze im Bereich der experimentellen Entwicklung vorangetrieben – und passgenaue, bionisch gestützte Konstruktionsmethoden bzw. Bauweisen erarbeitet werden. Durch die damit verbundene, deutliche Steigerung der Wirtschaftlichkeit, Ressourceneffizienz und Produktivität, kann eine signifikante Erweiterung und Diversifizierung der Einsatzfelder von endlosfaserverstärkten thermoplastischen Faserverbundmaterialien erzielt werden, wodurch intelligente und klimafreundliche Leichtbaulösungen in die breite industrielle Anwendung getragen werden. Aufgrund der großen Interdisziplinarität der Entwicklungsinhalte, wird – den förderpolitischen Zielen entsprechend – dabei ein branchenübergreifender Wissens- und Technologietransfer gefördert, wodurch ein wertvoller Betrag zur Sicherung des Industriestandortes Deutschland geleistet wird. Darüber hinaus kann das Vorhaben, wie in Kapitel V überschlägig dargestellt, einen maßgeblichen Betrag zur Erreichung der Klimaziele leisten.
Diese Projekt wurde gefördert durch: Bundesministerium für Wirtschaft und Klimaschutz und Projektmittelträger Jülich (PtJ)
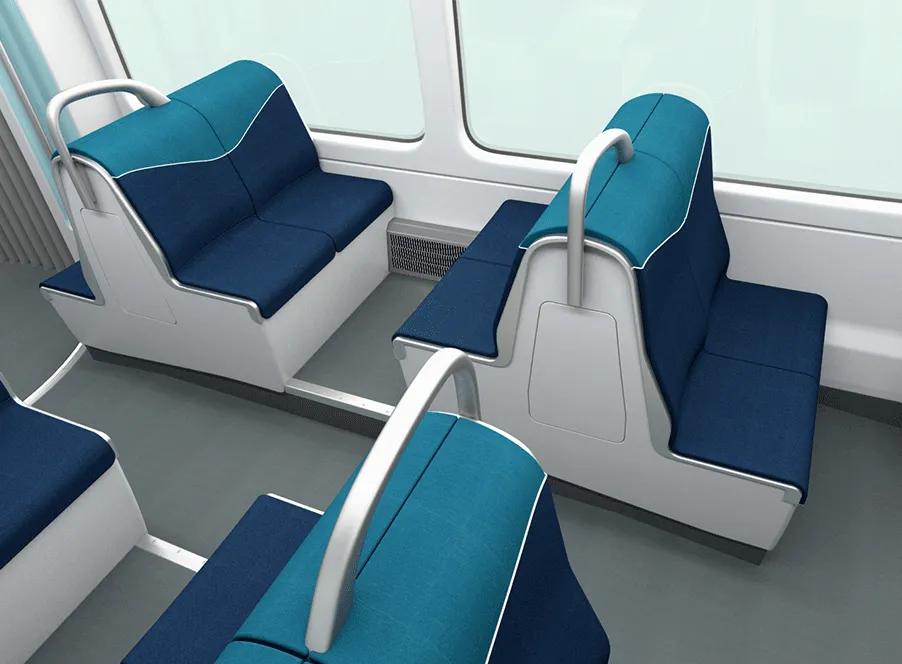
hybridBogie (abgeschlossenes Forschungsprojekt)
Mit dem Verbundprojekt hybridBOGIE entwickelte HÖRMANN Vehicle Engineering ein Drehgestell (DG) der neusten Generation. So entstand ein Drehgestell mit besseren Parametern in der Funktionalität, im Gewicht, in der Laufleistung und der Geräuschemission. Dies wurde durch die Erforschung einer Hybrid-Mischbauweise mit schwingungsdämpfenden Materialien und der aktiven Integration von Federungselementen in die Funktionsstruktur des Drehgestellrahmens (DGR) erreicht.
Ziel des Projektes war die Entwicklung eines Herstellungsprozesses zur Fertigung eines Hybridfaser-Drehgestellrahmens einschließlich des Demonstratoren- und Musterbaus. Außerdem ist die Auslegung und Einbindung eines Sensornetzes in den Drehgestellrahmen für eine permanente Bauteilüberwachung Bestandteil des Teilprojekts. Ebenfalls wurde ein Konzept zum Schutz der schlagempfindlichen Rahmenstruktur vor Steinschlag erforscht.
Dieses Projekt wurde gefördert durch: EFRE und SAB
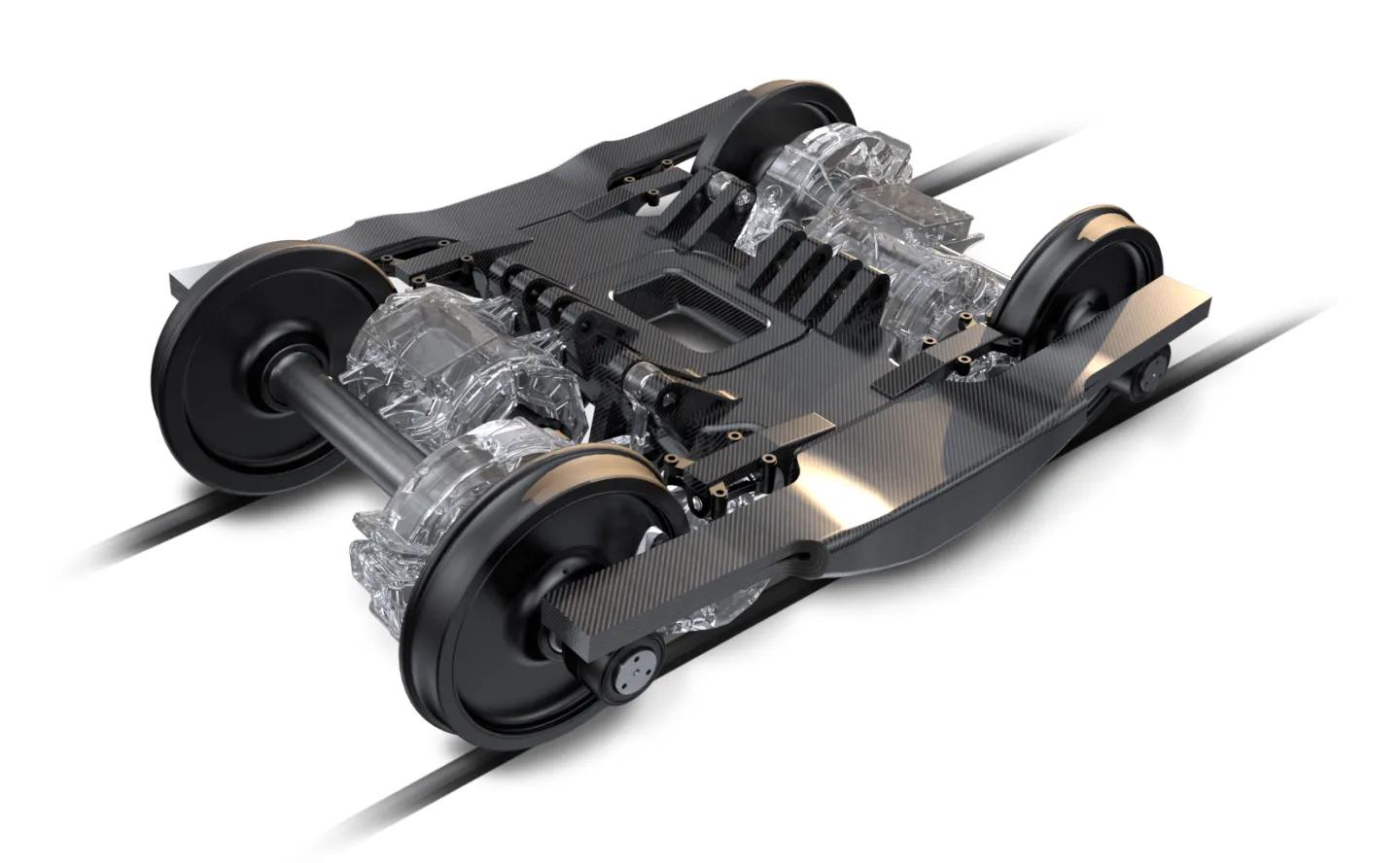
thermoPre plus (abgeschlossenes Forschungsprojekt)
Im Verbundprojekt mit regionalen Industriepartnern und Forschungseinrichtungen sollten leichte Faser-Kunststoff-Verbunde (FKV) mit ihren besonderen mechanischen Eigenschaften (Hochleistungspolymere) zu Halbzeugen, sogenannten Prepregs, verarbeitet werden und an Hochleistungsstrukturbauteile im Automobil und Schienenfahrzeugbau zum Einsatz kommen. Auf Basis neuartiger belastungsdedizierter Faserverbundstrukturen (effiload Halbzeuge) konzipierte HÖRMANN Vehicle Engineering als Verbundkoordinator einen einteiligen innovativen Straßenbahnsitz. Dieser ist 25 Prozent leichter als vergleichbare Sitzkomponenten und miniert den Montageaufwand erheblich . Solche thermoplastischen Faserverbundbauteile verfügen aufgrund ihrer kurzen Zykluszeiten bei der Bauteilherstellung über ein großes Potential für Serienanwendungen.
Diese Projekt wurde gefördert durch: Bundesministerium für Bildung und Forschung und Projektmittelträger Jülich (PtJ)
Innovatives Leichtbauchassis (abgeschlossenes Forschungsprojekt)
HÖRMANN Vehicle Engineering unterstützte die HÖRMANN Automotive GmbH bei der Entwicklung eines neuen Integral-Chassis-Konzept für leichte Nutzfahrzeuge. Das Konzept baut fertigungstechnologisch auf den Ergebnissen des erfolgreich abgeschlossenen Sonderforschungsbereichs 666 „Integrale Blechbauweisen höherer Verzweigungsordnung – Entwicklung, Fertigung, Bewertung“ der TU Darmstadt auf. Es bringt die dort erarbeiteten Technologien in eine Anwendung des Fahrzeugbaus für zukünftigen urbanen Lieferverkehr. Dabei nutzt es die verzweigten Blechstrukturen zur Realisierung neuer Schutzmechanismen für Energiespeicher von Fahrzeugen mit alternativen Antrieben.
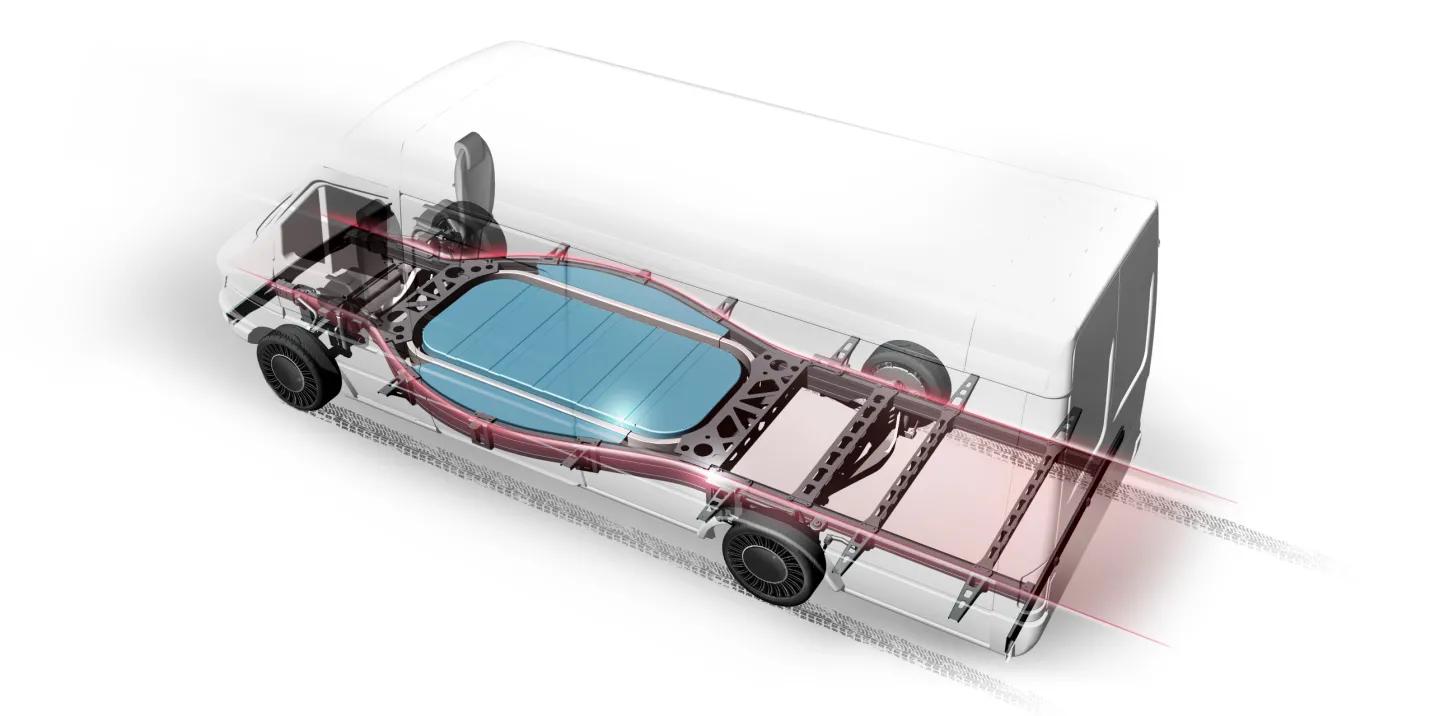